「需給情報の統合を実現する”S&OP” ~“インダストリー4.0”に向けた基盤固め~」
マネージャー 多田 和弘
- ■ 産業全体の情報連携
近年、IoT技術革新を背景に、モノや組織の情報連携を強化し、製造業の競争力を高めようとする国家的な取り組みが相次いで推進されている。こうした取り組みの代表格である「インダストリー4.0」は、2011年にドイツ政府が公布した高度技術戦略「ハイテク戦略2010行動計画」における戦略施策のひとつである。モノとサービスのインターネット(IoT)の製造プロセスへの応用により、生産プロセスの上流から下流までを垂直方向にネットワーク化し、あたかも一国の産業全体が一つの工場のように連携することで「第四次産業革命」の実現を目指している。
インターネットをモノづくりに導入する最大のメリットはそのリアルタイム性を最大限活用した生産拠点や企業の間の相互反応性の向上だ。具体的には、生産工程に関わる企業が、ネットを介して伝達される情報に反応して、生産・供給などの需給活動を自動的に行うことで、一企業ないし企業グループレベルを超え、産業単位でモノづくりの効率を極限まで高めようとしている。そしてこうした考え方は、今や本家のドイツのみでなく、IoT発祥の地であるアメリカはもとより、次世代のモノづくり大国としての覇権を競うインドをはじめとする新興国にも広がりを見せようとしている。日本においても、「日本版インダストリー4.0」とも言うべき各種研究や取り組みが官民問わず推進され始めている。
- ■ 需給情報の企業内統合の実態
一方、個々の企業が、インダストリー4.0で期待されているような産業レベルの情報連携に参画する際には、その企業内での取り扱われる情報が一元的に統合されていることが前提になることは言うまでもない。特に企業間連携における最重要情報ともいえる「需給情報(需要予測やそれに基づく販売計画、生産計画、調達計画ほか)」が、部署や組織ごとに異なっているようなことが起こっては、上記枠組みには参画すらできないことは容易に想像できるであろう。しかし、一見当たり前に見える需給情報の一元化を当たり前にできている企業は決して多くはない。私がこれまでのプロジェクトで見聞きしてきた経験に照らすと、むしろそれを実現している企業のほうが少ないのではないかとさえ感じる。
本稿では、インダストリー4.0に向けた対応を意識し始めた各企業において、まず具備すべき需給情報の一元化を阻む「構造的問題」を確認した上で、その対応方針および、実装方法案について論じる。
-
■ 各機能部門間の“相互不信”
同一製品に係る需給情報が統合されない理由のうち、メーカー実務に関与したことのある方に最も実感しやすいものは、生産や販売を担う各業務部門の、お互いの提示情報に対する“根深い不信感”によるものだろう。例えば営業部門は、多くの場合、工場(生産・調達機能を含む)が引き起こす欠品や納期遅延などに不信感を抱き、受注確度が低い段階から、「早め・多め」の販売計画を提示する。一方、生産部門は販売部門における計画確度の低さに起因する在庫過多を回避するため、不確かな情報に基づく独自の需要予測の結果、さらなる「早め・多め」生産計画を立案してしまう。調達部門はこの生産計画の不確実性のもと、部品の欠品によるさらなる生産遅れの発生を防ぐため、必要以上の部品在庫の山を築いてしまう。とりわけ、季節性の高い商品を扱う企業である場合、繁忙期と閑散期の生産能力ギャップの存在が、受注確度が不確かな段階からの「早め・多め」製造プレッシャーが働きやすく、生産・供給情報が多元化する温床となりやすい。
- ■ 経営/事業計画と業務(オペレーション)計画の“かい離”
機能部門間の相互不信といういわば、「業務レベル」に閉じた問題に加えて、「経営レベル」の問題も、生産・供給情報の一元化を阻む大きな要因となっている。
多くの企業において、経営層は事業分野ごとの売上や利益目標を“金額ベース”で設定し、目標達成のための経営計画を立案し、さらにそれを四半期や通年レベルまでブレークダウンしたものを事業計画や販売計画として展開している。これを受けた各機能部門は、この金額ベースの目標を達成するため、週次や月次で生産すべき製品の“数量ベース”計画に変換することで実行可能な計画に落とし込み、これをERPに代表される基幹業務システムなどで実行している。しかし、この金額ベース計画と数量ベース計画の精度の高いブレークダウンを、実需の状況や生産上の歩留まり変化などを勘案してリアルタイムに実施することは、従来の業務の枠組みやシステム機能で実施することは容易ではなく、全社合意のもと一意な数量計画が作られていないケースが多い。しかし、数量計画は生産や調達のオペレーションの遂行に必須であるため、各業務部門が独自の基準やタイミングでバラバラに策定され、同じ製品の生産・供給情報が、ともすれば関連部署の数だけ存在するという異常事態が生じるのだ。
-
■ 経営計画とオペレーション計画の統合
前述した部門間の相互不信や、経営と業務の分離により、需給情報の社内一元化が保てなくなっている企業に対する最も有力な処方箋は、経営と業務部門が“協働”して、皆が納得できる、“ただ一つの需給計画”を立案することである。
「S&OP(Sales & Operation Planning)」は、その名が示す通り、販売計画と、生産計画や調達計画などのオペレーション計画の統合を意味するコンセプトである。経営層が立案した金額ベースの事業計画を、製品カテゴリレベルの数量計画にブレークダウン、各種チャネルの販売力や生産キャパシティなども勘案し、複数のシナリオを検証した上で需給計画を確定する。営業や製造などの業務部門はそれを着実に実行するための部門計画を立案~遂行する(図1)。S&OPは1980年代に米国で提唱された、いわば“枯れた”概念であったが、情報技術の発展による実現性向上や導入コストの低廉化が進むと共に、近年改めて脚光を浴びるようになった。
図1:S&OPの考え方(イメージ)
(出所)NTTデータ経営研究所にて作成
- ■ 全世界で進むS&OP導入
S&OPの概念を最も早期の段階で理想的な形で実現したのは韓国のサムスンとされている。90年代に、PCメーカーのデルから吸収したSCMノウハウを独自に発展させ、2004年頃には、今日のS&OPのベースとなる計画統合を具現化したとされるが、近年ではこの考え方を模して、さまざまな企業がS&OP導入を進めている(表1)。
表1:近年のS&OP導入事例
(出所)
※1:月刊ロジスティックビジネス(2012/1、2014/3、2014/7)記事より抜粋
※2:SAP社ホームページ(http://www.sapjp.com/blog/archives/5029)より抜粋乳製品やベビーフードで世界最大のシェアを持つダノン・イタリア(同社は業務に関する権限を各国に委ねている)では、自社の営業施策(店頭値引きなどの販促活動)の効果を需要予測に反映できるシステムを導入し、その結果を生産計画や、物流センターから店頭への配送計画などに反映し、欠品による販売機会損失と廃棄ロスを極小化しているという。また、日本の精密機器メーカーであるコニカミノルタは、2003年に行われた経営統合以降、各社がそれぞれに構築していたサプライチェーンネットワークおよび、そのマネジメントプロセスの統合を段階的に高度化していく過程で、生産や販売の各拠点情報の数量実績を素早く金額ベースに換算、事業計画管理をタイムリーに実施できる仕組みを整えるに至っている。
また、ダノンやコニカミノルタなどの消費財メーカーのみならず、BtoBメーカーでもS&OP導入が進んでいる。大手鉄鋼メーカーJFEスチールでは、リーマンショックのようなグローバルな経済変動が、鉄鋼需要に急激かつ深刻な影響を及ぼすようになったことを背景に、より短い計画立案~実行オペレーションを実現すべく、営業・生産・物流に係る実行計画をシステム上で統合、これまで半期サイクルであった計画サイクルを月次まで短縮した。
世界的な化学メーカーであるデュポン社では、グローバルの生産計画・販売計画・製品計画(新製品/生産中止対象)・およびその結果である事業計画(予算)の4つの計画をクラウドシステム上で統合、12事業に渡る事業計画と45カ国に跨(またが)る207工場のオペレーション計画を一元管理することに成功しているという。
こうした導入事例を見ると、いずれの企業も、新規システムの導入ないし、既存システムの高度利用など、情報技術の活用により、S&OPを自社に実装しているケースが目立つ。実際に、S&OPというコンセプトと共に、その具現化を支援する(とされる)情報システムの紹介を受けた企業も多いことであろう。しかし、情報システムの導入に先んじて(または並行して)、自社の需給情報をどのように、どこまで一元化していくか、それをどのような方法論で実現するか?ということをしっかりと検討した上で、スコープを絞った社内トライアルの実施などを通じ、きちんと社内コンセンサスを取りながら地道に進めていくべきであろう。特に、事業計画や予算などの金額ベース計画と、オペレーション計画を統合するにあたっては、経営層や財務部門など、ステークホルダーが増えることに伴い、困難性が急激に上がる局面となる。そこを無理なく超えていくためには、まず「外堀」にあたる数量ベースの全社需要計画およびその元になるサプライチェーン情報の把握精度を十分に高めておいた上で、段階的に推進することをお勧めする(図2)。
図2:S&OPの段階導入(3か年導入ケース)
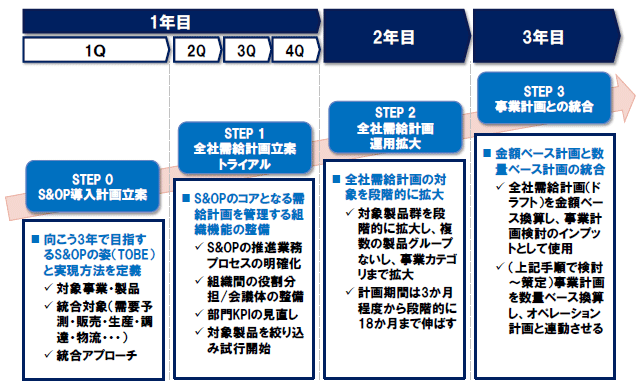
(出所)NTTデータ経営研究所にて作成
需給情報を企業内で統合することは、メーカーの業務そのものである“作って売る”行為を最も合理的に行うための基盤を整備することだ。インダストリー4.0が産業レベル・国家レベルのモノづくりの生産性を高めることができたとしても、その時に自社の競争力が落ちてしまっていては生き残れない。来るべき「インダストリー4.0時代」における産業間情報連携に向けた土台作りという意味でも、メーカーの最も重要な課題解決という意味でも、自社内の需給情報統合をきちんと、かつ無理なく、計画的に推し進めておきたい。
【多田和弘(ただかずひろ)】
大手鉄鋼メーカーにて自動車用鋼板などの生産管理に従事したのち、独系ERPベンダーにおける計画系システム導入を経て現職。主に事業会社における業務改革(BPR)推進・事業計画立案~実行支援・システムグランドデザイン構築、ITマネジメント推進等のコンサルティングに従事。